The Vacuum Lab at Karlsruhe Institute of Technology is where fundamental vacuum science meets applied process and technology development. Joe McEntee talks to the lab’s director Christian Day.

Christian Day is a vacuum scientist on a mission – almost evangelically so. As head of the Vacuum Lab at Karlsruhe Institute of Technology (KIT), part of Germany’s renowned network of federally funded Helmholtz Research Centres, Day and his multidisciplinary R&D team are putting their vacuum know-how to work in tackling some of society’s “grand challenges”.
Thinking big goes with the territory. As such, the KIT Vacuum Lab addresses a broad-scope canvas, one that acknowledges the core enabling role of vacuum technology in all manner of big-science endeavours – from the ITER nuclear-fusion research programme to fundamental studies of the origins of the universe (Day is also technical lead for cryogenic vacuum on the design study for the Einstein Telescope, a proposed next-generation gravitational-wave observatory).
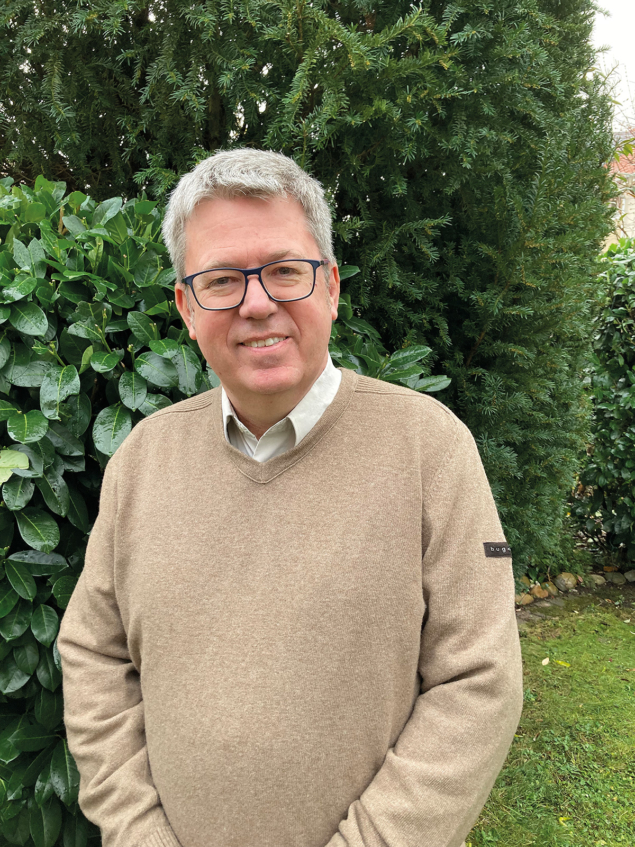
Here, Day tells CERN Courier about the Vacuum Lab’s unique R&D capabilities and the importance of an integrated approach to vacuum system development in which modelling, simulation and experimental validation all work in tandem to foster process and technology innovation.
What are the long-term priorities of the KIT Vacuum Lab?
Our aim is to advance vacuum science and technology along three main pathways: an extensive R&D programme in collaboration with a range of university and scientific partners; design and consultancy services for industry; and vacuum education to support undergraduate and postgraduate science and engineering students at KIT. It’s very much a multidisciplinary effort, with a staff team of 20 vacuum specialists working across physics, software development and the core engineering disciplines (chemical, mechanical, electrical). They’re supported, at any given time, by a cohort of typically five PhD students.
So what does that mean in terms of the team’s core competencies?
At a headline level, we’re focused around the two fundamental challenges in modern vacuum science: the realisation of a physically consistent description of outgassing behaviours for a range of materials and vacuum regimes; also the development of advanced vacuum gas dynamics methods and associated supercomputer algorithms.
As such, one of the main strengths of the KIT Vacuum Lab is our prioritisation of predictive code development alongside experimental validation – twin capabilities that enable us to take on the design, delivery and project-management of the most complex vacuum systems. The resulting work programme is nothing if not diverse – from very-large-scale vacuum pumping systems for nuclear fusion to contamination-free vacuum applications in advanced manufacturing (e.g. extreme UV lithography and solar-cell fabrication).
What sets the KIT Vacuum Lab apart from other vacuum R&D programmes?
Over the last 10 years or so, and very much driven by our contribution to the ITER nuclear fusion project in southern France, we have developed a unique and powerful software capability to model vacuum regimes at a granular level – from atmospheric pressure all the way down to extreme-high-vacuum (XHV) conditions (10–10 Pa and lower). This capability, and the massive computational resources that make it possible, are being put to use across all manner of advanced vacuum applications – quantum computing, HyperLoop transportation systems and gravitational-wave experiments, among others.
Mistakenly, early-career researchers often think that vacuum is a somehow old-fashioned service that they can buy off-the-shelf
The Vacuum Lab’s organising principles are built around “integrated process development”. What does that look like operationally?
It means we take a holistic view regarding the development of vacuum processes, which allows us to identify the main influences in the vacuum system and to map them theoretically or experimentally. An iterative design evolution must not only be based on efficient models; it must also be validated and parameterised by using experimental data from different levels of the process hierarchy. Experimental data are indispensable to evaluate the pros and cons of competing models and to quantify the uncertainties of model predictions.
In turn, the department’s research structure is set up to address elementary processes and unit functions within a vacuum system. When choosing a vacuum pump, for example, it’s important to understand how the pump design, underlying technology and connectivity will influence other parts of the vacuum system. It’s also necessary, though too often forgotten, for the end-user to understand the ultimate purpose of the vacuum system – the why – so that they can address any issues arising in terms of the vacuum science fundamentals and underlying physics.
What are your key areas of emphasis in fusion research right now?
Our vacuum R&D programme in nuclear fusion is carried out under the umbrella of EUROfusion, a consortium agreement signed by 30 research organisations and universities from 25 EU countries plus the UK, Switzerland and Ukraine. Collectively, the participating partners in EUROfusion are gearing up for the ITER experimental programme (due to come online in 2025), with a longer-term focus on the enabling technologies – including the vacuum systems – for a proof-of-principle fusion power plant called DEMO. The latter is still at the concept phase, though provisionally scheduled for completion by 2050.
As EUROfusion project leader for the tritium fuel cycle, I’m overseeing KIT’s vacuum R&D inputs to the DEMO fusion reactor – a collective effort that we’ve labelled the Vacuum Pumping Task Force and involving multiple research/industry partners. The vacuum systems in today’s nuclear fusion reactors – including the work-in-progress ITER facility – rely largely on customised cryosorption pumps for vacuum pumping of the main reaction vessel and the neutral beam injector (essentially by trapping gases and vapours on an ultracold surface). DEMO, though, will require a portfolio of advanced pumping concepts to be developed for ongoing operations, including metal-foil and mercury-based diffusion and ring pumps as well as high-capacity non-evaporable-getter (NEG) materials (see “Next-generation pump designs: from ITER to the DEMO fusion project”).
Next-generation pump designs: from ITER to the DEMO fusion project
By Yannick Kathage
When the ITER experimental reactor enters operation later this decade, nuclear fusion will be realised in a tokamak device that uses superconducting magnets to contain a hot plasma in the shape of a torus. Herein the fusion reaction between deuterium and tritium (DT) nuclei will produce one helium nucleus, one neutron and, in the process, liberate huge amounts of energy (that will heat up the walls of the reactor to be exploited in a power cycle for electricity production).
In this way, fusion reactors like ITER must combine large-scale vacuum innovation with highly customised pumping systems. The ITER plasma chamber (1400 m3), for example, will be pumped at fine vacuum (several Pa) against large gas throughputs in the course of the plasma discharge – the so-called burn phase for energy generation. There follows a dwell phase, when the chamber will be pumped down (for approximately 23 minutes) to moderately high vacuum (5 × 10–4 Pa), before initiating the next plasma discharge. Meanwhile, surrounding the plasma chamber is an 8500 m3 cryostat to provide a 10 mPa cryogenic insulation vacuum (required for the operation of the superconducting magnets).
A key design requirement for all of ITER’s pumping systems is to ensure compatibility with tritium, a radioactive hydrogen isotope. Effectively, this rules out the use of elastomer seals (only metal joints are permitted) and the use of oil or lubricants (which are destroyed by tritium contamination). Specifically, the six torus exhaust systems are based on so-called discontinuous cryosorption pumps, cooled with supercritical helium gas at 5 K and coated with activated charcoal as sorbent material to capture helium (primarily), a mix of hydrogen isotopes and various impurities from the plasma chamber.
As with all accumulation pumps, these cryopumps must be regenerated by heating on a regular basis. To provide a constant pumping speed on the torus during the plasma pulse, it’s therefore necessary to “build in” additional cryopumping capacity – such that four systems are always pumping, while the other two are in regeneration mode. What’s more, these six primary cryopumps are backed by a series of secondary cryopumps and, finally, by dry mechanical rough pumps that compress to ambient pressure.
Scaling up for DEMO
The operational principle of the cryosorption pump means that large quantities of tritium accumulate within the sorbent material over time – a safety concern that’s very much on the radar of the ITER management team as well as Europe’s nuclear regulatory agencies. Furthermore, this “tritium inventory” will only be amplified in the planned future DEMO power plant, providing real impetus for the development of new, and fully continuous, pumping technologies tailored for advanced fusion applications.
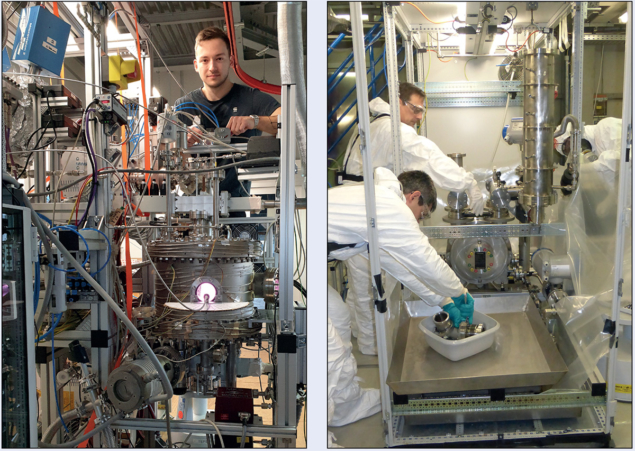
Among the most promising candidates in this regard is the so-called metal-foil pump (MFP), which uses a plasma source to permeate, and ultimately compress, a flux of pure hydrogen isotopes through a group V metal foil (e.g. niobium or vanadium) using an effect called superpermeation. The driving force here is an energy gradient in the gas species, up and downstream of the foil (due to plasma excitation, but largely independent of pressure). It’s worth noting that the KIT Vacuum Pumping Task Force initiated development work on the MFP concept five years ago, with a phased development approach targeting “mature technical exploitation” of superpermeation pumping systems by 2027.
If ultimately deployed in a reactor context, the MFP will yield two downstream components: a permeated gas stream (comprising D and T, which will be cycled directly back into the fusion reactor) and an unprocessed stream (comprising D, T, He and impurities), which undergoes extensive post-processing to yield an additional D, T feedstock. It is envisaged that both gas streams, in turn, will be pumped by a train of continuously working rough pumps that use mercury as a working fluid (owing to the metal’s compatibility with tritium). As the DEMO plant will feature a multibarrier concept for the confinement of tritium, mercury can also be circulated safely in a closed-loop system.
One of those alternative roughing pump technologies is also being developed by the KIT Vacuum Pumping Task Force – specifically, a full stainless-steel mercury ring pump that compresses to ambient pressure. Progress has been swift since the first pump-down curve with this set-up was measured (in 2013) and the task force now has a third-generation design working smoothly in the lab, albeit with all rotary equipment redesigned to take account of the fact that mercury has a specific weight 13 times greater than that of water (the usual operating fluid in a ring pump).
Hydrogen impacts
While mercury-based vacuum pumping is seen as a game-changer exclusively for fusion applications, it’s evident that the MFP is attracting wider commercial attention. That’s chiefly because superpermeation works only for the hydrogenic species in the gas mixture being pumped – thereby suggesting the basis of a scalable separation functionality. In the emerging hydrogen economy, for example, it’s possible that MFP technology, if suitably dimensioned, could be implemented to continuously separate hydrogen from the synthesis gas of classical gasification reactions (steam reforming) and at purities that can otherwise only be achieved via electrolytic processes (which require huge energy consumption).
Put simply: MFP technology has the potential to significantly reduce the ecological footprint associated with the mass-production of pure hydrogen. As such, once the MFP R&D programme achieves sufficient technical readiness, the KIT Vacuum Lab will be seeking to partner with industry to commercialise the associated know-how and expertise.
Yannick Kathage is a chemical engineering research student in the KIT Vacuum Lab.
How does all that translate into the unique facilities and capabilities within the KIT Vacuum Lab?

Our work on fusion vacuum pumps requires specialist domain knowledge regarding, for example, the safe handling of mercury as well as how to manage, measure and mitigate the associated radioactivity hazard associated with tritium-compatible vacuum systems. We have set up a dedicated mercury lab, for example, to investigate the fluid dynamics of mercury diffusion pumps as well as a test station to optimise their performance at a system level.
Many of the other laboratory facilities are non-standard and not found anywhere else. Our Outgassing Measurement Apparatus (OMA), for example, uses the so-called difference method for high-resolution measurements of very low levels of outgassing across a range of temperatures (from ambient to 570 K). The advantage of the difference method is that a second vacuum chamber, which is identical to the sample chamber, is used as a reference in order to directly subtract the background outgassing rate of the chamber.
Meanwhile, our TransFlow facility allows us to generate fluid flows at different levels of rarefaction, and across a range of channel geometries, to validate our in-house code development. Even TIMO, our large multipurpose vacuum vessel – a workhorse piece of kit in any vacuum R&D lab – is heavily customised, offering temperature cycling from 450 K down to 4 K.
What about future plans for the KIT Vacuum Lab?
A significant expansion of the lab is planned over the next four years, with construction of a new experimental hall to house a 1:1 scale version of the vacuum section of the DEMO fuel cycle. This facility – the catchily titled Direct Internal Recycling Integrated Development Platform Karlsruhe, or DIPAK – will support development and iteration of key DEMO vacuum systems and associated infrastructure, including a large vacuum vessel to replicate the torus – a non-trivial engineering challenge at 30 tonnes, 7 m long and 3.5 m in diameter.
How do you attract the brightest and best scientists and engineers to the KIT Vacuum Lab?
The specialist teaching and lecture programme that the vacuum team provides across the KIT campus feeds our talent pipeline and helps us attract talented postgraduates. Early-career researchers often think – mistakenly – that vacuum is somehow old-fashioned and a “commoditised service” that they can buy off-the-shelf. Our educational outreach shows them otherwise, highlighting no shortage of exciting R&D challenges to be addressed in vacuum science and technology – whether that’s an exotic new pumping system for nuclear fusion or a low-outgassing coating for an accelerator beamline.
The multidisciplinary nature of the vacuum R&D programme certainly helps to broaden our appeal, as does our list of high-profile research partners spanning fundamental science (e.g. the Weizmann Institute of Science in Tel Aviv), the particle accelerator community (e.g. TRIUMF in Canada) and industry (e.g. Leybold and Zeiss in Germany). Wherever they are, we’re always keen to talk to talented candidates interested in working with us.