When it becomes operational later this decade, the ITER fusion research project will be dependent on one of the most complex vacuum systems ever built. Joe McEntee checks out progress with ITER vacuum section leader Robert Pearce, while highlighting the downstream commercial opportunities already spinning out from the core construction programme.
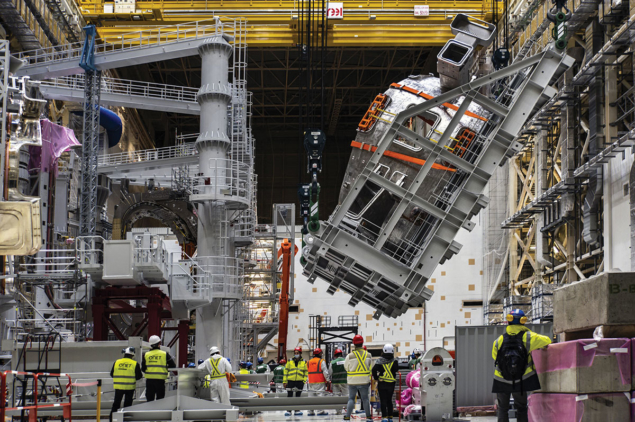
Robert Pearce is all about the detail. That’s probably as it should be for the section leader of the diverse, sprawling vacuum ecosystem now taking shape as part of the work-in-progress ITER experimental reactor in southern France. When it comes online in the mid-2020s, this collaborative megaproject – which is backed by China, the European Union, India, Japan, Korea, Russia and the US – will generate nuclear fusion in a tokamak device (the world’s largest) that uses superconducting magnets to contain and control a hot plasma in the shape of a torus. In the process, ITER will also become the first experimental fusion machine to achieve “net energy” – when the total power produced during a fusion plasma pulse surpasses the power injected to heat the plasma – while providing researchers with a real-world platform to test the integrated technologies, materials and physics regimes necessary for future commercial production of fusion-based electricity.

Vacuum reimagined
If ITER is big science writ large, then its myriad vacuum systems are an equally bold reimagining – at scale – of vacuum science, technology and innovation. “ITER requires one of the most complex vacuum systems ever built,” explains Pearce. “We’ve overcome a lot of challenges so far in the construction of the vacuum infrastructure, though there are doubtless more along the way. One thing is certain: we will need to achieve a lot of vacuum – across a range of regimes and with enabling technologies that deliver bulletproof integrity – to ensure successful, sustained fusion operation.”
The task of turning the vacuum vision into reality falls to Pearce and a core team of around 30 engineers and physicists based at the main ITER campus at Cadarache. It’s a multidisciplinary effort, with domain knowledge and expertise spanning mechanical engineering, modelling and simulation, experimental validation, surface science, systems deployment and integration, as well as process control and instrumentation. At a headline level, the group is focused on delivery versus two guiding objectives. “We need to make sure all the vacuum systems are specified to our exacting standards in terms of leak tightness, cleanliness and optimal systems integration so that everything works together seamlessly,” notes Pearce. “The other aspect of our remit involves working with multiple partner organisations to develop, validate and implement the main pumping systems, vacuum chambers and distribution network.”

Sharing the load
Beyond the main project campus, the two primary partners on the ITER vacuum programme are the Fusion for Energy (F4E) team in Barcelona, Spain, and US ITER in Oak Ridge, Tennessee, both of which support the vacuum effort through “in-kind” contributions of equipment and personnel to complement direct cash investments from the member countries. While the ITER Vacuum Handbook – effectively the project bible for all things vacuum – provides a reference point to shape best practice across vacuum hardware, associated control systems, instrumentation and quality management, there’s no one-size-fits-all model for the relationship between the Cadarache vacuum team and its partner network.
“We supply ‘build-to-print’ designs to Barcelona – for example, in the case of the large torus cryopump systems – and they, in collaboration with us, then take care of the procurement with their chosen industry suppliers,” explains Pearce. With Oak Ridge, which is responsible for provision of the vacuum auxiliary and roughing pumps systems (among other things), the collaboration is based on what Pearce calls “functional specification procurement…in which we articulate more of the functionality and they then work through a preliminary and final design with us”.
Vacuum innovation: ITER’s impact dividend
While ITER’s vacuum team pushes the boundaries of what’s possible in applied vacuum science, industry partners are working alongside to deliver the enabling technology innovations, spanning one-of-a-kind pumping installations to advanced instrumentation and ancillary equipment.
The ITER neutral beam injector systems – accelerators that will drive high-energy neutral particles into the tokamak to heat the fusion plasma – are a case in point. The two main injectors (each roughly the size of a locomotive) will be pumped by a pair of open-structure, panel-style cryosorption pumps (with a single pump measuring 8 m long and 2.8 m high).
Working in tandem, the pumps will achieve a pumping speed of 4500 m3/s for hydrogen, with a robust stainless-steel boundary necessary for the cryogenic circuits to provide a confinement barrier between tritium (which is radioactive) and cryogenic helium.
Key to success is a co-development effort – involving ITER engineers and industry partner Ravanat (France) – to realise a new manufacturing method for the fabrication of cryopanels via expansion of stainless-steel tube (at around 2000 bar) into aluminium extrusions. It’s a breakthrough, moreover, that delivers excellent thermal contact over the operating temperature range (4.5 K for pumping to 400 K for regeneration), while combining the robustness of stainless steel with the thermal conductivity of aluminium.
Industry innovation is also in evidence at a smaller scale. As the ITER project progresses to the active (nuclear) phase of operations, for example, human access to the cryostat will be very limited. With this in mind, the In-Pipe Inspection Tool (IPIT) is being developed for remote inspection and leak localisation within the tens of km of cryostat pipework.
An R&D collaboration between ITER vacuum engineers, F4E and Italian robotics firm Danieli Telerobot, the IPIT is capable of deployment in small-bore pipework up to 45 m from the insertion point. The unit combines a high-resolution camera for inspection of welds internal to the pipe, as well as a dedicated “bladder” for isolation of vacuum leaks prior to repair.
Other instrument innovations already well developed by industry to meet ITER’s needs include a radiation-hardened (> 1 MGy) and magnetic-field-compatible (> 200 mT) residual gas analyser that permits remote operation via a controller up to 140 m away (supplied by Hidden Analytical, UK); and also an optical diaphragm gauge (> 1 MGy, > 200 mT) with a measurement capability in line with the best capacitive manometers (a co-development between Inficon, Germany, and OpSens Solutions, Canada).
When it comes to downstream commercial opportunities, it’s notable that ITER member countries share the experimental results and any intellectual property generated by ITER during the development, construction and operation phases of the project.
More broadly, because vacuum is central to so many of ITER’s core systems – including the main tokamak vessel (1400 m3), the surrounding cryostat (16,000 m3) and the superconducting magnets – the vacuum team also has touch-points and dependencies with an extended network of research partners and equipment makers across ITER’s member countries. Unsurprisingly, with more than 300 pumping systems and 10 different pumping technologies to be deployed across the ITER plant, complexity is one of the biggest engineering challenges confronting Pearce and his team.
“Once operational, ITER will have thousands of different volumes that need pumping across a range of vacuum regimes,” notes Pearce. “Overall, there’s high diversity in terms of vacuum function and need, though the ITER Vacuum Handbook does help to standardise our approach to issues like leak tightness, weld quality, testing protocols, cleanliness and the like.”

Atypical vacuum
Notwithstanding the complexity of ITER’s large-scale vacuum infrastructure, Pearce and his team must also contend with the atypical operational constraints in and around the fusion tokamak. For starters, many of the machine’s vacuum components (and associated instrumentation) need to be qualified for operation in a nuclear environment (the ITER tokamak and supporting plant must enclose and securely contain radioactive species like tritium) and to cope with strong magnetic fields (up to 7 T in the plasma chamber and up to 300 mT for the vacuum valves and instruments). In terms of qualification, it’s notable that ITER is being built in a region with a history of seismic activity – deliberately so, to demonstrate that a fusion reactor can be operated safely anywhere in the world.
“Ultimately,” concludes Pearce, “any vacuum system – and especially one on the scale and complexity required for ITER – requires great attention to detail to be successful.”