In November 1972, CERN’s Roger Calder described in detail the unprecedented vacuum system of the world’s first hadron collider, the Intersecting Storage Rings.
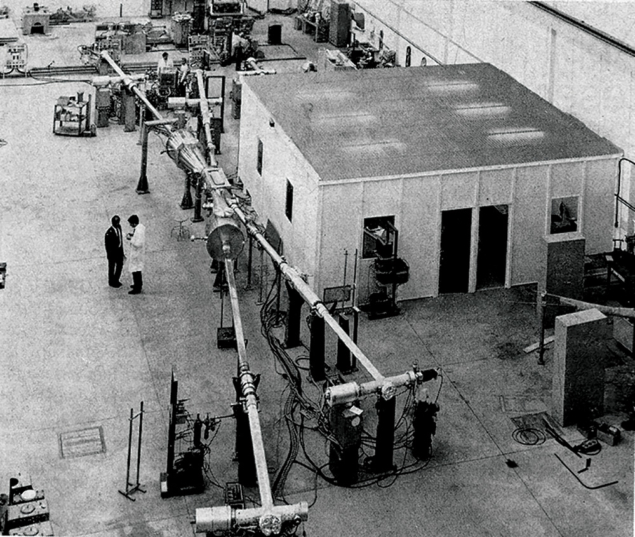
The vacuum system of the CERN Intersecting Storage Rings differs from those of typical particle accelerators in one vital respect: the pressure has to be four to five orders of magnitude lower. This requirement can be readily understood in terms of the time ratio the particles spend circulating (of the order of one second in an accelerator and, typically, one day in the ISR). It would be an exaggeration to say that the problem of attaining this vacuum was more difficult in the same ratio but it was considerably more difficult and involved many basically different techniques. Some of these were known on a small scale from the laboratory, others had to be developed.
A major triumph of the ISR vacuum system has been the successful marrying of many hitherto specialised laboratory techniques into one very large and very complex system without loss in reliability or performance. It is still not unusual to find ultra-high vacuum laboratories which have difficulty in working at 10–11 torr – in the ISR there are hundreds of metres at this pressure and soon it is expected to extend to the full 2 kilometres of the rings.
This article will try to sketch some of the problems encountered in meeting the requirements of the vacuum system and how the applied research in this field led to their solution.
Sources of gas
The pressure in a vacuum system, in the simplest analysis, is given by the balance between the residual gas inflow rate and the exhaust rate. The latter, determined by the size and speed of the vacuum pumps, is limited by available space and cost. The former is the sum of several sources including leaks from the surrounding atmosphere, desorption of gas which has been adsorbed on the interior surface of the vacuum chamber and the permeation of gas through the chamber material itself.
Assuming that all leaks have been eliminated – in itself not a trivial problem since these may range from leaky joints to microscopic pores via slag inclusions in the chamber material – and that surface desorption has been reduced to a negligible value by in situ bakeout of the vacuum system at 300 °C, there is left what perhaps appears the negligible possibility of gas permeating through the metal chambers. In fact, this constitutes the major limitation in a vacuum system such as the ISR where the available pumping speed is severely restricted by the low conductance of the chamber.
The chamber material is a nitrogen enriched austenitic stainless steel chosen on the basis of mechanical strength, low permeability, good vacuum properties, etc. Careful measurements showed that this material, even after an in situ bakeout at 300 °C, was releasing hydrogen gas at the rate of about 3.10–12 torr litre per second per cm2 (equivalent to about 108 hydrogen molecules per second per cm2). The measurements also showed that this hydrogen appeared to be diffusing out of the bulk of the material (rather than desorbing from the surface) and the constancy of the rate over long times suggested a virtually infinite reservoir of hydrogen. This was confirmed by chemical analysis which showed the hydrogen impurity to be about 0.001% or 1019 molecules per cm3 of steel.
This outgassing rate would have caused unacceptably large pressures in the beam pipe between pumping stations – pressures which could not be reduced by larger pumps but only by reducing the outgassing rate by one to two orders of magnitude. Laboratory measurements showed that the diffusion rate, and hence the outgassing rate, was very temperature dependent. This suggested a way of removing the source of hydrogen – the steel was subjected to a heat treatment of about 1000 °C in a vacuum furnace before being used. At this temperature the hydrogen release is so fast that the concentration of dissolved hydrogen falls rapidly to a value determined by the partial pressure in the vacuum furnace. In this way it was possible to obtain the tons of stainless steel with special low outgassing rates which were needed for the ultra-high vacuum system of the ISR.
Cryopumping for even lower pressure
In addition to the ultra-high vacuum requirement of 10–10 to 10–11 torr all around the ISR rings, dictated essentially by beam life-time considerations, the experimenters would like the intersection regions with pressures in the 10–12 torr range or better. Such low pressures reduce the ratio of the background signals due to proton–gas molecule collisions compared to the true proton–proton collisions. Pressures even into the 10–13 torr range have been obtained, notably in intersection region 1-6, using cryopumping techniques.
In a cryopumped intersection region a surface is cooled to a low temperature and acts as a trap to ‘solidify’ any gas molecule which strikes it. The speed of the pump depends on the area of the cooled surface (12 l/s and 45 l/s per cm2 of surface are possible pumping rates for nitrogen and hydrogen respectively) and the pressure limit depends on the temperature of the surface and the gas (lower temperatures are needed the lower the boiling point of the gas).
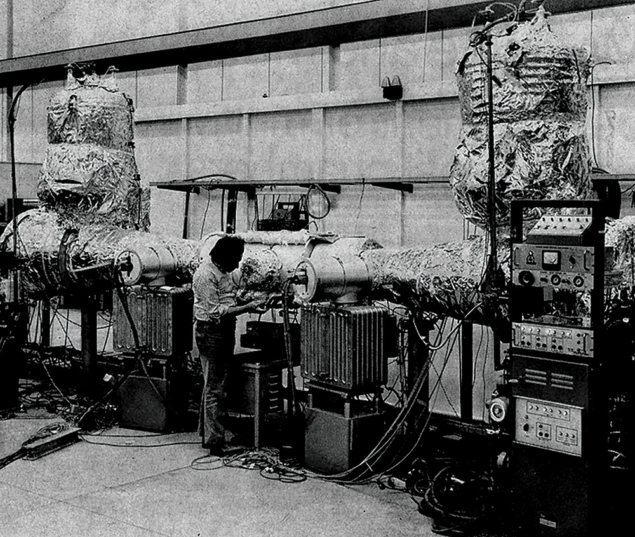
Hydrogen, as described above, is the major gas load in the ISR; unfortunately it is the most difficult gas to condense apart from helium. The theoretical low pressure limit of a cryopump is given by the saturated vapour pressure of the gas being condensed at the temperature of the pumping surface. For hydrogen this is still about 10–6 torr at 4.2 K (a convenient refrigeration temperature using liquid helium as coolant) but it should fall to an extrapolated value of 10–13 torr at 2.5 K. In practice, however, it proved impossible to condense hydrogen to pressures below about 10–10 torr, independently of what temperature was used. This anomaly was traced to an interaction between the (black body) thermal radiation coming from the vacuum chambers at room temperature and the condensed hydrogen layer – the latter being continually desorbed by this thermal bombardment. The interaction is not one of simple heating but depends in a complex way on the thickness and purity of the condensed layer and on the characteristics of the cold substrate carrying the condensed layer.
Although it was possible to operate a liquid helium cooled cryopump down to 10–13 torr in the laboratory even when exposed to thermal radiation by modifying the substrate (e.g. by the precondensation of an inert gas layer of argon or neon) a more practical solution has been developed and used in the ISR. This involves using optically and almost thermally opaque chevron baffles at 77 K which are optimised for molecular transmission. This is a compromise involving a considerable loss of conductance, and hence pumping speed, to the vacuum chamber. The pump and baffles are thus designed to achieve a given pressure and then dimensioned to give the required pumping speed. Two liquid helium cooled cryopumps have been installed in 1-6. Each has a speed of about 15 000 l/s and a limit pressure of about 2.10–13 torr. They have operated for several months in the upper 10–13 torr range.
Measuring very low pressures
An advance in one technique often exposes a weakness in another. It was noticed that laboratory systems, designed to extend knowledge of very low pressures, frequently appeared to be limited at about 1 to 2.10–12 torr. Nearly all very low pressure gauges use a tungsten filament heated to about 2300 °C to provide a source of ionising electrons. The apparent limit pressures were traced to an artefact introduced by the gauge itself – the vapour pressure of tungsten evaporated from the heated tungsten filament. Operating the filament at a carefully chosen and reduced temperature can extend the useful range of the gauge by almost an order of magnitude.
The hot tungsten filament is at the root of another problem. It produces heating in the surrounding vacuum chamber causing an increase of hydrogen desorption and a real increase of the system pressure. Recent development work has shown that it will be possible to construct an extremely sensitive gauge using the high gain of an integral channel electron multiplier. The gauge should be useful down to 10–15 torr and, since it uses an extremely low ionising current of a few nanoamperes, it will produce practically no heating or disturbance to the vacuum system.
Beam induced vacuum problems
‘Pressure bumps’ in the ISR have been in the news before (see vol. 11, page 245). They are the major obstacle to achieving the design stored beams of 20 A and the design luminosity. They are localised regions of about 10 m in which the pressure, normally stable at about 10–10 torr in the absence of the beam, begins to rise when the stacked proton beam current exceeds a certain value. Pressure bumps may occur anywhere around either ring at one or several points simultaneously. The mechanism is one of gas release from the wall of the vacuum chamber under ion bombardment. The ions, formed by the ionising effect of the proton beam on the 10–10 torr of residual gas, are ejected out of the space charge potential of the beam onto the wall with an energy of about 1 keV. The released gas increases the local pressure and thus gives, in turn, more ions. Hence we have the makings of an avalanche effect and the pressure may stabilise at some higher value or increase without limit until it destroys the stacked beam.
The danger is obviously greatest where the residual pressure is greatest, where the pumping speed is lowest or where the vacuum chamber wall is contaminated and there is a large gas yield per incident ion. It is now clear that, even after the elaborate cleaning and degassing procedures, the vacuum chamber is not as clean as was thought. On the basis of thermally induced desorption, it had been concluded that hydrogen dissolved in the metal is the only source of gas. But now it is apparent that the surface is covered with a layer of strongly adsorbed contaminants (H2, H2O, CO, CO2, CH4, hydrocarbons etc.) which are only released under energetic ion bombardment.
During the initial operation of the ISR the critical current for run-away pressure bumps was about 4 A. At that time the 10–10 torr operating pressure was achieved after an in situ bakeout of about 4 hours at 200 °C. Since then the temperature has been raised to 300 °C and the bakeout time lengthened to about 24 hours – the critical currents have climbed to 10 to 12 A. The normal operating pressure is still about 10–10 torr but clearly the surfaces now appear much cleaner under ion bombardment.
Why stop there ? Because many components of the ISR were designed for a maximum bakeout temperature of 300 °C, and further increase of the bakeout times at constant temperature seems to give practically no advantage. Other parameters have to be attacked – those of residual pressure and pumping speed. All the intersection regions were initially equipped with titanium sublimation pumps in addition to the normal sputter-ion pumps, which are the standard pumping element around the ISR. Pressures at the intersections were typically around 2.10–11 torr and the ‘pressure bump’ phenomenon rarely occurred in these regions.
A vacuum improvement programme is therefore under way to equip the whole of the ISR with additional sublimation pumps. They are installed in eleven of the 24 sectors which operate regularly at 2.10–11 torr. Pressure bumps in the unimproved sectors still limit the performance but there are high hopes of reaching the design current early next year when the whole vacuum system is improved and running at 2.10–11 torr.
In the meantime extensive laboratory investigations are under way to find ways of eliminating surface contamination. The most promising approach at the moment seems to be to simulate and accelerate the ion-induced desorption by running a high pressure (10–2 torr) inert gas discharge in the vacuum chamber. Subsequent gas release rates on test samples have been reduced by two or even three orders of magnitude by this technique. But there is a technical problem – how to propagate and control a gas discharge around 2 kilometres of ISR vacuum chamber. At the same time, more sophisticated cleaning and bakeout techniques, new surface treatments or even the possibility of a new chamber of an altogether different material is under study.
The results of applied research in the fields of materials science, low temperature physics, ultra-high vacuum technology and engineering have helped to create in the ISR the largest ultra-high vacuum system ever built. Exciting specialised techniques, such as cryopumping at 2.5 K have been integrated with everyday nuts and bolts in their thousands. Possibly the most important achievement of the ISR vacuum system is the extremely high reliability of many apparently commonplace components – there are over 10 000 demountable flanges, for example, which must all be leak-tight simultaneously. This reliability is the result of careful and thorough applied research. There are still problems – such as the pressure bumps but, to (mis-) quote from the Shakespeare play which gave us our title, ‘Think not on it till tomorrow: we’ll devise thee brave punishments for it’.
- This article was adapted from text in CERN Courier vol. 12, November 1972, pp359–362