
The new year at CERN has seen good news for two types of magnet that will be essential to focusing beams in the Large Hadron Collider (LHC). One of them, the first US-built magnet, came 6000 km by land and sea from the Brookhaven National Laboratory in New York. The other, a matching quadrupole magnet (MQM), built by UK firm Tesla Engineering, is showing exceptional performance levels.
The Brookhaven-built magnet, which arrived at CERN on 21 January, is a 10 m long, 4.7 tonne single-aperture dipole. Magnets of this type will be installed on either side of the ALICE and LHCb experiments to deviate the beams in order to make them interact and then to separate them. This first example, manufactured over a period of nine months by Brookhaven, is one of 20 magnets that the US laboratory is supplying for the “insertion regions” (where beams are deviated for various reasons), and includes four of the same type as the new arrival at CERN. The magnets are based on a technology developed by Brookhaven for its own RHIC accelerator.
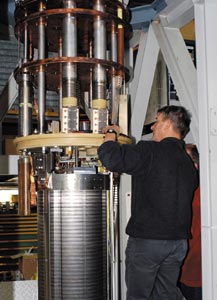
LHC project leader Lyn Evans said: “Our Brookhaven colleagues have done a fantastic job in completing the USA’s first superconducting magnet for the LHC to specification and on schedule. It’s a great step forward for international collaboration in the construction and operation of large-scale installations for particle physics research.” Indeed, Brookhaven is not the only American partner in the LHC project, to which the US is contributing a total of $531 million (€490 million). Fermilab is building 18 “low-beta” quadrupole magnets, and the Lawrence Berkeley National Laboratory is working on the superconducting cable and feed boxes for the same quadrupoles.
The MQMs from the UK are also destined for the LHC’s eight insertion zones. The first 3.5 m long superconducting MQM has been undergoing stringent operating tests at CERN, reaching a magnetic field gradient of 215 T/m from the very first time it was powered up – under normal operating conditions it will only be required to reach 200 T/m, and the ramping took place without a single quench. This excellent result validates the choice of design and the industrial techniques, so series production can now begin.