From the HL-LHC magnets to the ITER fusion project, Stefano Sgobba, Katie Buchanan and Ana Teresa Perez Fontenla describe how CERN deals with complex demands for mechanical design, production facilities and material science at CERN and beyond.
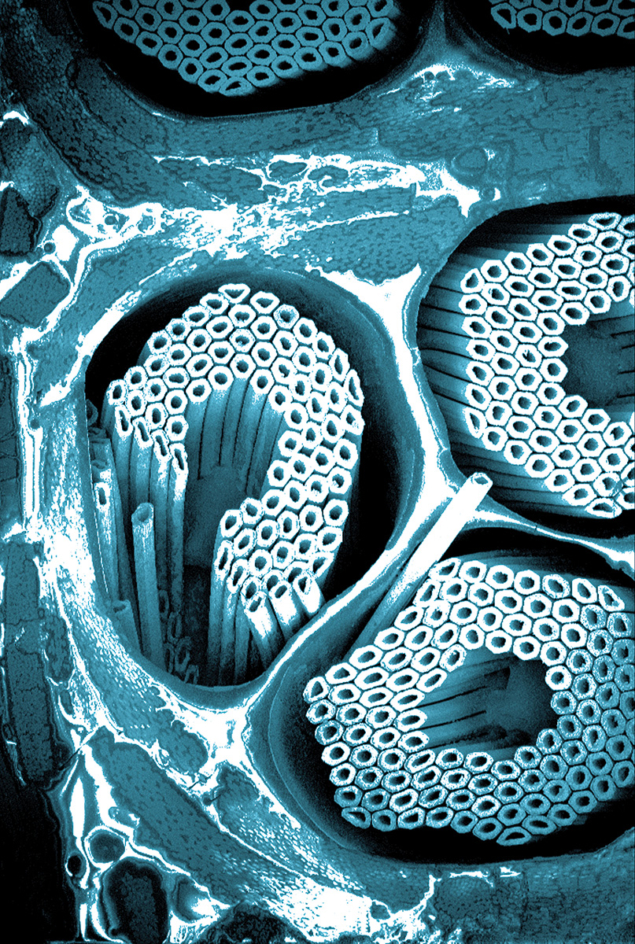
The nature of CERN’s research often demands unusual and highly complex materials to be developed and tested. A good example is the LHC beam screen that limits the energy transfer from the beam to the cold mass of the magnets, for which a new non-magnetic stainless steel had to be developed in the mid-1990s to meet the physical and mechanical requirements at cryogenic temperatures. The same is true of the external cylinder of the CMS solenoid magnet, for which a process enabling the production of 7 m-diameter high-strength seamless aluminium-alloy rings had to be identified and qualified. Another breakthrough at the LHC has been the solution adopted for the end covers of the cold masses of the dipole magnets, for which 2500 stainless-steel powder metallurgy-hot isostatic pressed covers were produced – qualifying this innovative shaping solution for the first time for massive, fully reliable leak-tight operation at cryogenic temperatures.
Similar challenges apply today for the High-Luminosity LHC (HL-LHC), which is due to operate from 2029. For the HL-LHC radio-frequency crab cavities, which will tilt the beams at the collision points to maximise the luminosity, niobium and niobium-titanium alloy products have been carefully identified and qualified. Niobium additive-manufactured at CERN achieved a record purity and conductivity for this kind of product. For the new HL-LHC magnets, which are necessary to focus the beams more tightly at the collision points, detailed qualifications of the soundness of niobium-tin (Nb3Sn) coils have been critical, as has the development and qualification of methods to test the weld of the quadrupole magnet cold masses.
These and numerous other projects are the domain of the CERN materials, metrology and non-destructive testing (EN–MME–MM) section, whose mission is to provide material sciences for accelerators and detectors spanning the whole CERN community, in close coordination with the mechanical design and production facilities of the EN-MME group. The interdisciplinary, expert-staffed section guarantees a full life-cycle management of materials – from functional requirements to prototyping, series production, inspection and end-of-life – and includes the identification or development of material solutions, the specification and qualification of suppliers, the definition of manufacturing and inspection plans, and inspections of received materials and parts before and after their integration into the machines and experiments. This challenging mission requires advanced microscopic materials analysis, high-precision optical metrology, mechanical static and cyclic measurements, including at cryogenic temperatures, and, last but not least, state of the art non-destructive testing techniques (see “Section facilities” figure).
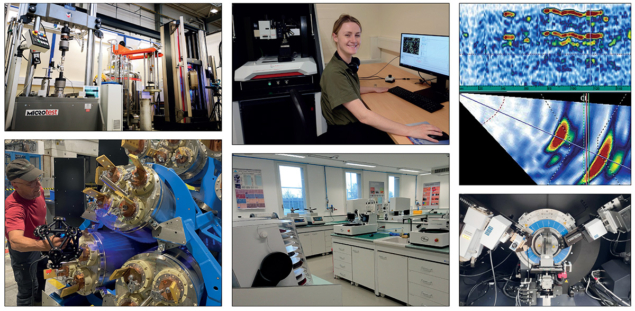
High-field magnets
The future of particle accelerators is strongly linked to the development of high–field superconducting magnets that enable higher energies and luminosities to be attained. The HL-LHC will be the first operational facility to employ high-performance Nb3Sn accelerator magnets, surpassing the intrinsic performance limitations of NbTi-based magnets as used for the LHC. The fabrication of Nb3Sn magnets is a challenging process because the conductor is an extremely brittle intermetallic phase. While the difficulty of working with brittle compounds is reduced using the traditional wind-react-and-impregnate approach, uncertainties remain due to volume changes associated with phase transformations occurring during the reaction heat treatment necessary to form the Nb3Sn phase.
Needle in a haystack
To investigate the root causes of performance limitation or degradation observed on early magnets, several HL-LHC dipole and quadrupole magnet coils were examined. This project has been one of the most complex failure analyses ever undertaken by the MM section, demanding an innovative investigation methodology to be identified and performed at several fabrication stages and after cool-down and powering. Internal shear and bending loads on unsupported superconducting wires, which can cause their dislocation as well as cracks in the aggregates of Nb3Sn filaments, were suspected to be the main cause of limitation or degradation. Like hunting for a needle within a massive haystack, the challenge was to find microscopic damage at the level of the filaments in the large volume of coils covering a length up to 7.2 m.
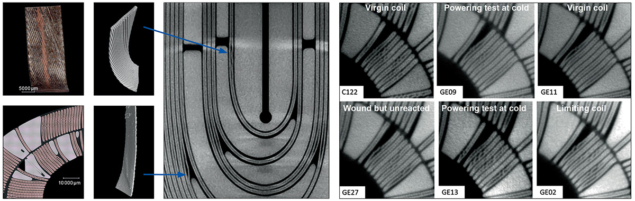
Starting in 2020 with 11 T magnet-coil ends, a sequence of mesoscale observations of whole coil sections was carried out non-destructively using innovative high-energy X-ray computed tomography (CT). This enabled the critical volumes to be identified and was followed up with a microscopic assessment of internal events, geometrical distortions and potential flaws using advanced microscopy. As a result, the MM section was able to unequivocally identify strands with transversely broken elements (see “Dipole diagnostics” and “Cracking niobium tin” figures). Techniques such as scanning electron microscopy (SEM) and focussed ion beam (FIB) were used to analyse damage to strands or sub-elements at particular localised positions as well as failure modes. In addition, a deep-etching technique allowed a decisive observation of completely broken filaments (see “HL-LHC coils up close” figure). Taken together, this comprehensive approach provided an in-depth view of the examined coils by identifying and characterising atypical features and imperfections in both the superconducting phase of the strands and the glass fibre/resin insulation system. It also clearly associated the quenches (a sudden loss of the superconducting state) experienced by the coils with physical events, namely broken superconducting filaments or damaged strands. The successful analysis of the CERN coil limitations led the MM section to receive several coils from different non-conforming quadrupole magnets, fabricated in the US in the framework of the Accelerator Upgrade Project collaboration, and successfully carry out the same type of investigations.

Effective recovery
This highly effective approach and key results on Nb3Sn accelerator magnets were made possible thanks to the wide experience gained with previous applications of CT techniques to the magnet system of the ITER fusion experiment, which employs the Nb3Sn conductor on a massive scale. The aim of such investigations is not only to understand what went wrong, no matter how difficult and complex that might be, but also to identify remedial actions. For the HL-LHC magnets, the MM section has contributed widely to the introduction of effective recovery measures, improved coil manufacturing and cold-mass assembly processes, and the production of magnets with reproducible behaviour and no sign of degradation. These results led to the conclusion that the root cause of the performance limitation of previous long CERN magnets has been identified and can now be overcome for future applications, as is the case for Nb3Sn quadrupole magnets.
Structural support
Investigating the massive HL-LHC coils required a highenergy (6 MeV) linac CT that was subcontracted to TEC Eurolab in Italy and Diondo GmbH in Germany, two of only a few companies in the world that are equipped with this technique. However, the MM section also has an X-ray CT facility with an energy of 225 keV, which enables sufficient penetration for less massive samples. One of the most recent of countless examples employing this technique concerns the staves for the future ATLAS tracker (ITk) for the HL-LHC upgrade. During 2023 a significant fraction of the ITk modules suffered from early high-voltage breakdowns, despite appearing to perform satisfactorily during earlier stages of quality control. A subset of these modules exhibited breakdowns following thermal cycling, with some failing during the cold phases of the cycle. Additionally, others experienced breakdowns after being loaded onto their supporting staves. High-resolution CT scans at CERN combined with other techniques confirmed the presence and propagation of cracks through the entire sensor thickness, and enabled the MM team to identify the gluing process between the carbon structure and the sensors as the root cause of the vulnerability, which is now being addressed by the ATLAS project team (see “ATLAS modules” figure). Also for the HL-LHC, the section is working on the internalisation process of the beryllium vacuum-chamber fabrication technology required for the experiments.
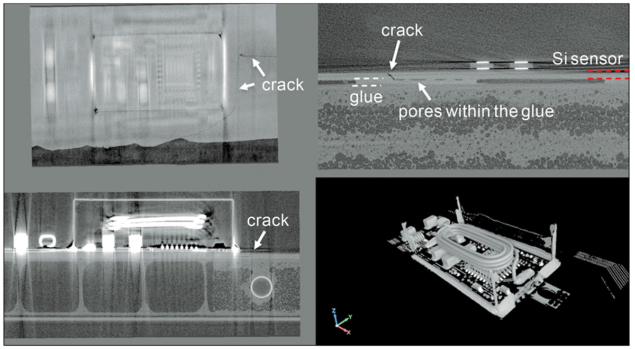
While carrying out failure analyses of extremely high-tech components is the core business of the MM section, in some cases understanding the failure of the most basic objects can be paramount. This does not necessarily mean that the investigations are simpler. At 11 a.m. on 13 October 2022, a pipe supplying CERN with water burst under the main road near the French–Swiss border, which was closed until early afternoon. The damage was quickly repaired by the Swiss services, and the road re-opened. But it was critical to understand if this was an isolated incident of an individual pipe, in service for 20 years, or if there was the potential risk of bursts in other ducts of the same type.
The services of the MM section, provided via cooperation agreements with CERN, are in wide demand externally
The damaged portion of the duct, measuring 1.7 m in length and 0.5 m in diameter, is the largest sample ever brought to the MM facilities for root-cause analysis (see “Water pipe” figure). As such, it required most of the available techniques to be deployed. For the receiving inspections, visual and radiographic testing and high-precision optical dimensional metrology in a volume of almost 17 m3 were used. For microstructural examinations, tests by CT, microoptical and SEM observations on the samples surrounding the crack – including a post-resin burn-off test – were carried out. The cracking (one of the most common found in water and sewer pipes) turned out to be the result of bending forces due to local soil movement. This generated a flexural constraint between the supported ends of the failing section, consisting of a concrete base on one side and a connection sleeve to the next pipe section on the opposite side. The change of boundary conditions may have been due to droughts during summer periods that altered the soil conditions. To the great relief of all, the composite material of the pipe or its constituents were not the main cause of the failure.
Beyond CERN
The services of the MM section, provided via cooperation agreements with CERN, are also in wide demand externally. ITER is a strong example. As of 2009, a major multi-year cooperation agreement is in place specifically covering metallurgical and material testing for the construction of the ITER magnet and vacuum systems. The many results and achievements of this long-lasting cooperation include: the qualification of high-strength stainless-steel jacket material for the conductor of the ITER central solenoid, including their cryogenic properties; the development and application of advanced examination techniques to assess the vacuum pressure impregnation process used in the correction coils and their critical welds, which are not inspectable with conventional techniques; and the assessment of a high-strength austenitic stainless steel for the precompression structure of the central solenoid, involving forgings featuring an unprecedented combination of size and aspect ratio. The section has also been fully entrusted by the ITER organisation for major failure analysis, such as the root-cause analysis of a heavy gauge fastener of the toroidal-field gravity support system and, more recently, the analysis of leakage events in the thermal-shield cooling pipes of the ITER magnet system. Several agreements are also in place via the CERN knowledge transfer group for the assessment of structural materials for a fusion project beyond ITER, and for a subcritical fission reactor project.
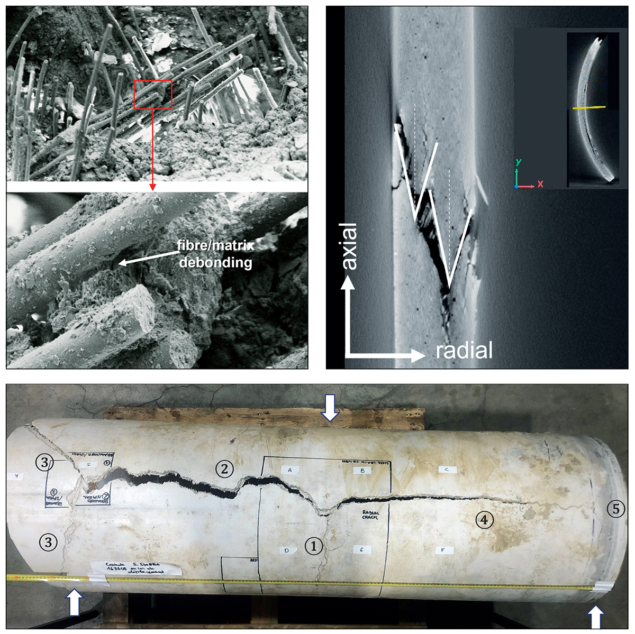
Also not to be forgotten is the major involvement of CERN in the Einstein Telescope project, for example in assessing suitable materials and fabrication solutions for its vacuum system, one of the largest ultra-high vacuum systems ever built. A three-year-long project that started in September 2022 aims to deliver the main technical design report for the Einstein Telescope beampipes, in which CERN’s contribution is structured in eight work packages spanning design and materials choice to logistics, installation and surface treatments (CERN Courier September/October 2023 p45).
Beyond fundamental physics, the section is also working on the selection of materials for a future hydrogen economy, namely the definition of the proper specification and procedures for operation in a liquid-hydrogen environment. The watchmaking industry, which places high requirements on materials, also cooperates in this field. It is expected that the section will also receive requests for even more collaboration projects for different fields.
It is quite true to say that materials are everywhere. The examples given here clearly show that in view of the ambitious goals of CERN, a highly interdisciplinary effort from materials and mechanical engineers is paramount to the proper selection and qualification of materials, parts and processes to enable the creation of the giant colliders and detectors that allow physicists to explore the fundamental constituents of the universe.