The challenges in building a new light source.

Image credit: NSRRC.
On 31 December, commissioning of the Taiwan Photon Source (TPS) at the National Synchrotron Radiation Research Center (NSRRC) brought 2014 to a close on a highly successful note as a 3 GeV electron beam circulated in the new storage ring for the first time. A month later, the TPS was inaugurated in a ceremony that officially marked the end of the 10-year journey since the project was proposed in 2004, the past five years being dedicated to the design, development, construction and installation of the storage ring.
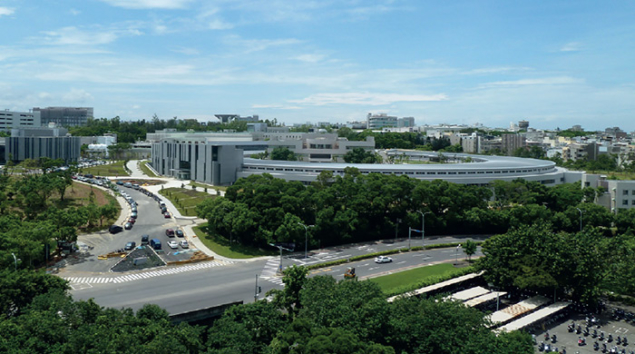
Image credit: NSRRC.
The new photon source is based on a 3 GeV electron accelerator consisting of a low-emittance synchrotron storage ring 518.4 m in circumference and a booster ring (CERN Courier June 2010 p16). The two rings are designed in a concentric fashion and housed in a doughnut-shaped building next to a smaller circular building where the Taiwan Light Source (TLS), the first NSRRC accelerator, sits (see cover). The TLS and the new TPS will together serve scientists worldwide whose experiments require photons ranging from infrared radiation to hard X-rays with energies above 10 keV.
Four-stage commissioning
The task of commissioning the TPS comprised four major stages involving: the linac system plus the transportation of the electron beam from the linac to the booster ring; the booster ring; the transportation of the electron beam from the booster ring to the storage ring; and, finally, the storage ring. Following the commissioning of the linac system in May 2011, the acceptance tests of key TPS subsystems progressed one after the other over the next three years. The 700 W liquid-helium cryogenic system, beam-position monitor electronics, power supplies for quadrupole and sextupole magnets, and two sets of 2 m-long in-vacuum undulators completed their acceptance tests in 2012. Two modules of superconducting cavities passed their 300 kW high-power tests. The welding, assembly and baking of the 14 m-long vacuum chambers designed and manufactured by in-house engineers were completed in 2013. Then, once the installation of piping and cable trays had begun, the power supply and other utilities were brought in, and set-up could start on the booster ring and subsystems in the storage ring.
The installation schedule was also determined by the availability of magnets. By April 2014, 80% of the 800 magnets had been installed in the TPS tunnel, allowing completion of the accelerator installation in July (bottom right). Following the final alignment of each component, preparation for the integration tests of the complete TPS system in the pre-commissioning phase was then fully under way by autumn.
The US$230 million project (excluding the NSRRC staff wages) involved more than 145 full-time staff members
The performance tests and system integration of the 14 subsystems in the pre-commissioning stage started in August. By 12 December, the TPS team had begun commissioning the booster ring. The electron beam was accelerated to 3 GeV on 16 December and the booster’s efficiency reached more than 60% a day later. Commissioning of the storage ring began on 29 December. On the next day, the team injected the electrons for the first time and the beam completed one cycle. The 3 GeV electron beam with a stored current of 1 mA was then achieved and the first synchrotron light was observed in the early afternoon on 31 December (far right). The stored current reached 5 mA a few hours later, just before the shut down for the New Year holiday. As of the second week of February 2015, the TPS stored beam current had increased to 50 mA.
The US$230 million project (excluding the NSRRC staff wages) involved more than 145 full-time staff members in design and construction. Like any other multi-million-dollar, large-scale project, reaching “first light” required ingenious problem solving and use of resources. Following the groundbreaking ceremony in February 2010, the TPS project was on a fast track, after six months of preparing the land for construction. Pressures came from the worldwide financial crisis, devaluation of the domestic currency, reduction of the initial approved funding, attrition of young engineers who were recruited by high-tech industries once they had been trained with special skills, and bargaining with vendors. In addition, the stringent project requirements left little room for even small deviations from the delivery timetable or system specifications, which could have allowed budget re-adjustments.
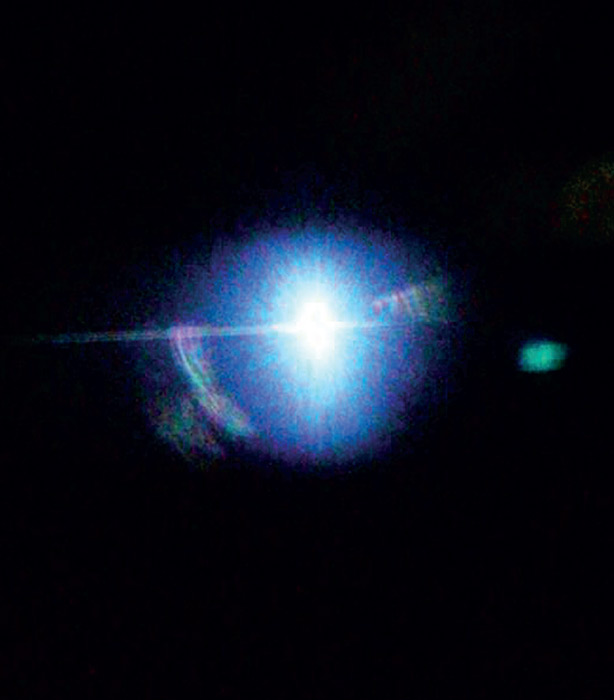
Image credit: NSRRC.
To meet its mandate on time, the project placed reliance and pressure on experienced staff members. Indeed, more than half of the TPS team and the supporting advisors had participated in the construction of the TLS in 1980s. During construction of the TPS, alongside the in-house team were advisers from all over the world whose expertise played an important role in problem solving. In addition, seven intensive review meetings took place, conducted by the Machine Advisory Committee.
From the land preparation in 2010 onwards, the civil-construction team faced daily challenges. For example, at the heart of the Hsinchu Science Park, the TPS site is surrounded by heavy traffic, 24 hours a day, all year round. To eliminate the impact of vibration from all possible sources, the 20 m wide concrete floor of the accelerator tunnel is 1.6 m thick. Indeed, the building overall can resist an earthquake acceleration of 0.45 g, which is higher than the Safe Shutdown Earthquake criteria for US nuclear power plants required by the US Nuclear Regulatory Commission.
The civil engineering took an unexpected turn at the very start when a deep trench of soft soil, garbage and rotting plants was uncovered 14 m under the foundations. The 100 m long trench was estimated to be 10 m wide and nearly 10 m thick. The solution was to fill the trench with a customized lightweight concrete with the hardness and geological characteristics of the neighbouring foundations. The delay in construction caused by clearing out the soft soil led to installation of the first accelerator components inside the TPS shielding walls in a dusty, unfinished building with no air conditioning. The harsh working environment in summer, with temperatures sometimes reaching 38 °C, made the technological challenges seem almost easy.
Technology transfer
The ultra-high-vacuum system was designed and manufactured by NSRRC scientists and engineers, who also trained local manufacturers in the special technique of welding, the clean-room setup, and processing in an oil-free environment. This transfer of technology is helping the factories to undertake work involving the extensive use of lightweight aluminum alloy in the aviation industry. During the integration tests, the magnetic permeability of the vacuum system in the booster ring, perfectly tailored for the TPS, proved not to meet the required standard. The elliptical chambers were removed immediately to undergo demagnetization heat-treatment in a furnace heated to 1050 °C. For the 2 m long components this annealing took place in a local factory, while shorter components were treated at the NSRRC. The whole system was back online after only three weeks – with an unexpected benefit. After the annealing process, the relative magnetic permeability of the stainless vacuum steel chambers reached 1.002, lower than the specification of 1.01 currently adopted at light-source facilities worldwide.
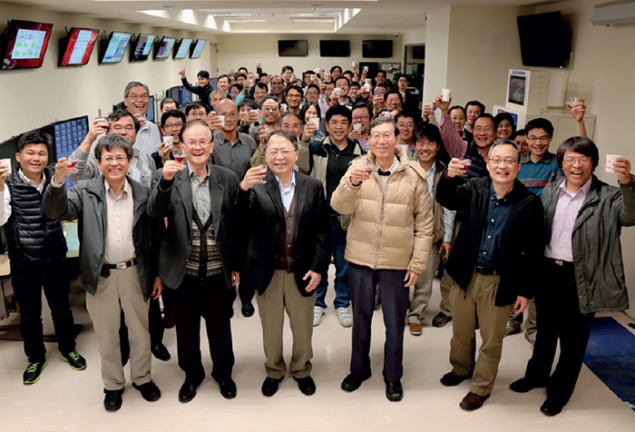
Image credit: NSRRC.
The power supplies of the booster dipole magnets were produced abroad and had several problems. These included protection circuits that overheated to the extent that a fire broke out, causing the system to shut down during initial integration tests in August. As the vendor could not schedule a support engineer to arrive on site before late November, the NSRRC engineers instead quickly implemented a reliable solution themselves and resumed the integration process in about a week. The power supplies for the quadrupole and sextupole magnets of the storage ring were co-produced by the NSRRC and a domestic manufacturer, and deliver a current of 250 A, stable to less than 2.5 mA. Technology transfer from the NSRRC to the manufacturer on the design and production of this precise power supply is another byproduct of the TPS project.
24-hour shifts
Ahead of completion of the TPS booster ring, the linac was commissioned at a full-scale test site built as an addition to the original civil-construction plan (CERN Courier July/August 2011 p11). The task of disassembling and moving the linac to the TPS booster ring, re-assembling it and testing it again was not part of the initial plan in 2009. The relocation process nearly doubled the effort and work time. As a result, the four-member NSRRC linac team had to work 24-hour shifts to keep to the schedule and budget – saving US$700,000 of disassembly and re-assembly fees had this been carried out by the original manufacturer. After the linac had been relocated, the offsite test facility was transformed into a test site for the High-Brightness Injector Group.
Initially, the TPS design included four superconducting radiofrequency (SRF) modules based on the 500 MHz modules designed and manufactured at KEK in Japan for the KEKB storage ring. However, after the worldwide financial crisis in 2008 caused the cost of materials to soar nearly 30%, the number of SRF modules was reduced to three and the specification for the stored electron beam was reduced from 400 mA to 300 mA. But collaboration and technology transfer on a higher-order mode-damped SRF cavity for high-intensity storage rings from KEK has allowed the team at NSRRC to modify the TPS cavity to produce higher operational power and enable a stored electron beam of up to 500 mA – better, that is, than the original specification. (Meanwhile, the first phase of commissioning in December used three conventional five-cell cavities from the former PETRA collider at DESY – one for the booster and two for the storage ring – which had been purchased from DESY and refurbished by the NSRRC SRF team.)
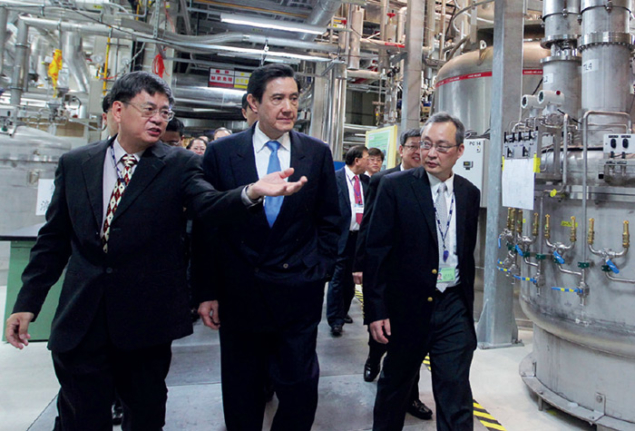
Image credit: Office of the President.
The TPS accelerator uses more than 800 magnets designed by the NSRRC magnet group, which were contracted to manufacturers in New Zealand and Denmark for mass production. To control the electron beam’s orbit as defined by the specification, the magnetic pole surfaces must be machined to an accuracy of less than 0.01 mm. At the time, the New Zealand factory was also producing complicated and highly accurate magnets for the NSLS-II accelerator at Brookhaven National Laboratory. To prevent delays in delivering the TPS magnets – a possible result of limited factory resources being shared by two large accelerator projects – the NSRRC assigned staff members to stay at the overseas factory to perform on-site inspection and testing at the production line. Any product that failed to meet the specification was returned to the production line immediately. The manufacturer in New Zealand also constructed a laboratory that simulated the indoor environment of the TPS with a constant ambient temperature. Once the magnets reached an equilibrium temperature corresponding to a room temperature of 25°C in the controlled laboratory, various tests were conducted.
Like the linac, the TPS cryogenic system was commissioned at a separate, specially constructed test site. The helium cryogenic plant was dissembled and reinstalled inside the TPS storage ring in March 2014, followed by two months of function tests. With the liquid nitrogen tanks situated at the northeast corner, outside and above the TPS building, feeding the TPS cooling system – which stretches more than several hundred metres – is a complex operation. It needs to maintain a smooth transport and a long-lasting fluid momentum, without triggering any part of the system to shut down because of fluctuations in the coolant temperature or pressure. The cold test and the heat-load test of the liquid helium transfer-line is scheduled to finish by the end of March 2015 so that the liquid helium supply will be ready for the SRF cavities early in April.
Since both the civil engineering and the construction of the accelerator itself proceeded in parallel, the TPS team needed to conduct acceptance tests of most subsystems off-site, owing to the compact and limited space in the NSRRC campus. When all of the components began to arrive at the yet-to-be completed storage ring, the installation schedule was planned mainly according to the availability of magnets. This led to a two-step installation plan. In the first half of the ring, bare girders were set up first, followed by the installation of the magnets as they were delivered and then the vacuum chambers. For the second half of the ring, girders with pre-mounted magnets were installed, followed by the vacuum chambers. This allowed error-sorting with the beam-dynamics model to take place before finalizing the layout of the magnets for the minimum impact on the beam orbit. Afterwards, the final alignment of each component and tests of the integrated hardware were carried out in readiness for the commissioning phase.
Like other large-scale projects, leadership played a critical role in the success of completing the TPS construction to budget and on schedule. Given the government budget mechanism and the political atmosphere created by the worldwide economic turmoil over the past decade, leaders of the TPS project were frequently second-guessed on every major decision. Only by having the knowledge of a top physicist, the mindset of a peacemaker, the sharp sense of an investment banker and the quality of a versatile politician, were the project leaders able to guide the team to focus unwaveringly on the ultimate goal and turn each crisis into an opportunity.