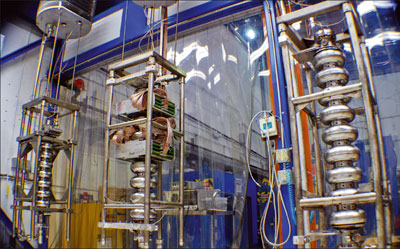
Image credit: Jefferson Lab.
For the first time, a US-industry-made superconducting radiofrequency (SRF) cavity has reached and exceeded the accelerating gradient required for the envisioned International Linear Collider (ILC). The cavity achieved 41 MV/m at the ILC’s superconducting operating temperature of 2 K, thus far exceeding the specification of the ILC Global Design Effort (GDE) of 35 MV/m. The ILC would require about 16,000 such cavities.

Image credit: Jefferson Lab.
Advanced Energy Systems Inc (AES) in Medford, New York, built the hollow niobium accelerating structure. A team at the Jefferson Lab processed it by electropolishing and then tested it as part of R&D funded by the US Department of Energy. In addition, they tested seven more AES cavities, one of which reached 34 MV/m, close to the specification. Several other North American companies are also attempting to manufacture ILC test cavities.
Jefferson Lab’s Rongli Geng, leader of the GDE Cavity Group, characterizes the 41 MV/m result as “remarkable”. He believes that it may be attributable to improvements in cavity treatment specific to AES cavities, which are aimed at optimizing the properties of the materials. Such optimization provides opportunities to attack the performance limitations of SRF cavities and improve the production yield in a realm other than processing and fabrication.
One such opportunity may have appeared during Jefferson Lab’s testing of AES cavities in conjunction with the heat treatment that removes hydrogen from cavity surfaces. Both the successful cavity and the one that was nearly successful underwent quicker, hotter heat treatment than had previously been standard: 2 hours at 800 °C instead of 10 hours at 600 °C. Because the AES-built cavities appeared to be stiffer, the revised treatment temperature primarily targeted the optimization of mechanical properties. However, because other improvements in material properties might also have occurred, the team at Jefferson Lab is conducting further investigations.
New temperature-mapping and optical-inspection tools adopted about a year ago under the guidance of ILC GDE project managers may also help to overcome the performance limitations of SRF cavities and improve the mass-production yield. “T-mapping” of cavity outer surfaces involves strategically placing thermal sensors to provide vital information about excessive heating in defective regions up to the point of local breakdown of superconductivity that causes a cavity to quench. This diagnostic procedure works in conjunction with the optical inspection of the surfaces within a cavity, which involves a mirror and a long-distance (around 1 m) microscope that together afford detailed mirror-reflected views of defective regions magnified at scales of about 0.1–1 mm.