Dispatches from two US labs that are helping to build the advanced magnets and “crab” cavities for the High-Luminosity LHC.
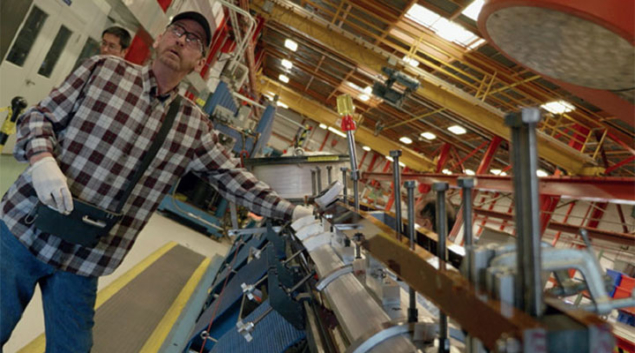
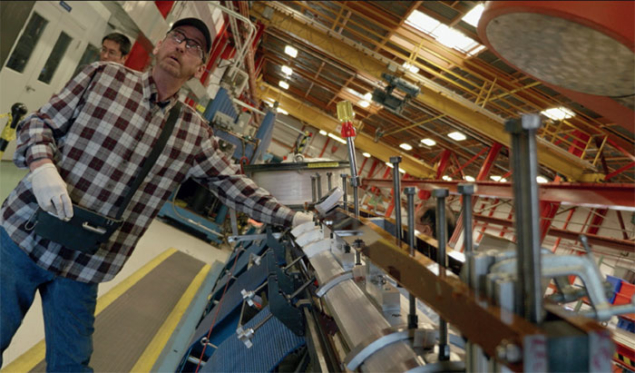
All image credits: J Ordan/CERN.
Inside the IB3 Tech Building at Fermilab on the outskirts of Chicago, a heavy-duty machine several metres long slowly winds a flat superconducting cable. Watching the bespoke coil winder – called the Spirex and manufactured by Italian firm SELVA – in action, and the meticulous attention to detail from the coil’s specialist operators, is mesmerising. Their task is to fabricate the precision coils that will form the core of novel magnets for CERN’s High-Luminosity LHC (HL-LHC) project, scheduled to begin operation in the early 2020s. “It has to make 50 turns in total, 22 on the inner layer and 28 on the outer,” explains Fred Nobrega, of Fermilab’s magnet-systems department. The main challenge is the niobium-tin (Nb3Sn) material, he says. “Bend it and it breaks like spaghetti.”
The HL-LHC magnets will be built from Nb3Sn, a new conductor used for the first time in an accelerator. Unlike copper, however, Nb3Sn is extremely brittle. Winding turns around the ends of the coil is particularly difficult, says Nobrega, and new chemical and heat treatments are being developed in the current R&D phase of the project at Fermilab to address this issue. The aim is to move from the prototype stage directly to the mass production of 45 long coils that are uniform and of high quality. A further 45 coils will be manufactured more than 1000 km away at Brookhaven National Laboratory (BNL).
The HL-LHC relies on a number of innovative magnet and accelerating technologies, most of which are not available off-the-shelf. Key to the new accelerator configuration are powerful superconducting dipole and quadrupole magnets with field strengths of 11 and 12 T, respectively (for comparison, the superconducting niobium-titanium dipoles that guide protons around the existing LHC have fields of around 8.3 T. The new quadrupoles will be installed on either side of the LHC collision points to increase the total number of proton–proton collisions by a factor 10, therefore boosting the chances of a discovery. Although the project requires modifications to just 5% of the current LHC configuration (see article on p28), each one of the HL-LHC’s key innovative technologies pose exceptional challenges that involve several institutes around the world.
Magnets of choice
Fermilab has a glorious history in superconductivity. It was here that the first large superconducting magnet accelerator was built, for example. “But more than that, it was shown that [superconducting magnets] could be reliably employed in a collider experiment for hours and hours of stable beams,” says physicist Giorgio Bellettini, who was spokesperson of the CDF experiment at Fermilab’s Tevatron collider during the mid-1990s at the time the top quark was discovered there. “The LHC experience is built upon this previous large endeavour.”
The plan is to develop and build half of the focusing magnets for the HL-LHC in the US. These have the specific project labels Q1 and Q3, and are a collaboration between three laboratories: Fermilab, BNL and Lawrence Berkeley National Laboratory in California. Nb3Sn technology, whose development has been supported by the US Department of Energy, was not applicable to accelerator magnets until around a decade ago. Now, Nb3Sn magnets are the technology of choice. The prototypes being developed here are 4 m long, and once assembled with the surrounding “cold mass” to keep them below the superconducting operational temperature of Nb3Sn, they will grow to around twice this length.
The innovative feature of these magnets is their very large aperture – 150 mm in diameter – which is necessary to focus the proton beams more tightly in the interaction points. It also allows greater control of the stress on the magnets and the coils induced by the large magnetic field, explains Giorgio Apollinari, who joined Fermilab in the early days and is now director of the US LHC Accelerator Research Program (LARP). No magnet today can achieve fields of 12 T with such a big opening, which is three times larger than that of the existing LHC dipoles. This is a new development introduced by the LARP team, explains Apollinari, and it took several years to go from 70, then 90 to 120 and now 150 mm required by the HL-LHC. “And then you have to have all the infrastructure necessary to build the magnets, test the magnets, make sure they work, measure the field quality and hopefully send them to CERN for installation in the beamline in 2025.”
Fermilab and the other LARP laboratories have successfully built 1 m-long short models to demonstrate that the technology meets the technical requirements, and the components are working exactly as expected. Now the teams are building longer prototypes with the correct length, aperture and all other design features. The next step is to build a full prototype with four coils, to complete the quadrupole configuration of the magnets, this coming spring. Similar magnets are being prototyped at CERN with a more ambitious length of 7.5 m. The final product from the US will be a 60 cm-diameter 4 m-long basic magnet containing a hole for the HL-LHC beam pipe. Twenty of these structures will be built in total, 10 in the US and 10 at CERN, of which 16 will be installed and the rest kept as spares. “This is collaboration in physics at its best,” explains Apollinari. “Everybody is trying to go faster, but we are looking at what each other does openly and learning from each other.”
Focus on cavities
Over at Fermilab’s sister laboratory, Argonne National Laboratory (ANL) some 40 km away, the other substantial part of the US contribution to the HL-LHC project is gathering pace. This involves novel “crab”-cavity technology, which is needed both to increase the luminosity and reduce so-called beam–beam parasitic effects that limit the collision efficiency of the accelerator. Unlike standard radiofrequency cavities, which accelerate charged particles in the direction along their path, crab cavities provide a transverse deflection of the beam which causes it to rotate.
The cavities are made from pure niobium and therefore require strict control from contamination via chemical processing. ANL specialises in superconducting cavities with a wide range of geometries, and a joint facility for the chemical processing of cavities is in place. ANL’s extensive experience with superconducting cavities includes the Argonne Tandem Linac Accelerator System (ATLAS). Built and operated by the physics division, this is the world’s first superconducting linear accelerator for heavy ions, working at energies in the vicinity of the Coulomb barrier to study the properties of the nucleus. It is for this machine that niobium was used for the first time in an accelerator, in 1977, and for which “quarter-wave” superconducting cavities were developed. “We developed superconducting cavities for a whole variety of projects, for the ATLAS accelerator, Fermilab, BNL, SLAC and of course for the HL-LHC at CERN,” says ANL accelerator scientist Michael Kelly. We meet in the lobby of the ANL physics division, next to a piece of the laboratory’s history: Enrico Fermi’s original “chopper”, a mechanical rotating shutter to select neutrons built in 1947 as part of ANL’s original nuclear-physics programme. “Today we process crab cavities for the HL-LHC, trying to achieve the highest possible accelerating or crabbing voltages, by making a very very clean surface on the cavity,” he explains.
ANL’s chemical processing facility has recently been enlarged to accommodate new buffer chemical polishing and electro-polishing rooms. Wearing a complete set of clean-room garments as we enter the facility, electronic engineer Brent Stone explains the importance of surface processing. “A feature of niobium is that a damaged layer is formed as it is mined from the ground and goes through all different processes, so when the niobium is transformed into cavities we need to remove a 120–150 μm-thick damaged layer,” he says. “Inside these layers you can have inclusions that may affect their performance and it is critical to remove them.”
Several steps, and journeys, are required to process the cavities. After the application of acids to remove material from the surface, the cavities undergo two cycles in ultrasonic tanks before being rinsed at high pressure and returned to Fermilab to be degassed in vacuum at high temperatures. They are then taken back to ANL for final chemical treatment, cleaning and assembly in the clean room. Finally, the cavities processed at Argonne are sent to BNL were they are cooled down to liquid-helium temperatures to test if they meet the crabbing voltage required for the HL-LHC. “One of the cavities processed has just very easily achieved its design goal,” says Kelly proudly, before we take leave of the laboratory.
Next stop CERN
The crab cavities are less advanced than the magnets for the HL-LHC, both at CERN and at Fermilab. But efforts are progressing on schedule on both sides of the Atlantic. Two different designs have been developed for the HL-LHC interaction points: vertical plane for ATLAS and horizontal plane for CMS. Both cavity designs originated from LARP, the LHC accelerator R&D programme created by the DOE in 2005 while the LHC was nearing its completion. “Without that foresight we wouldn’t have the HL-LHC today,” says Apollinari.