As Matthew Chalmers reported in 2017, completion of the first toroidal-field coil for ITER demonstrates niobium-tin superconductor technology on a gigantic scale.
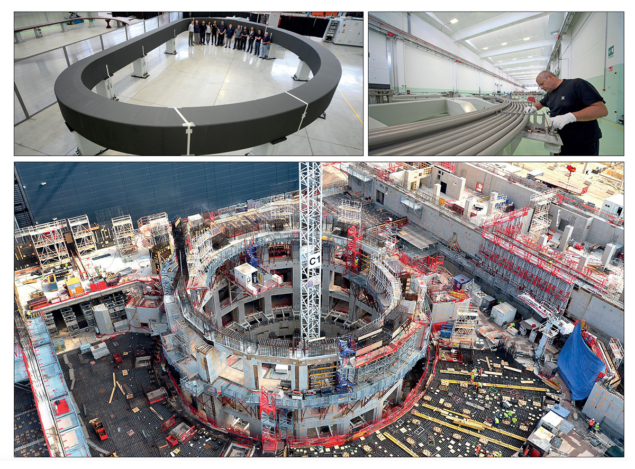
It is 14 m high, 9 m wide and weighs 110 tonnes. Fresh off a production line at ASG in Italy, and coated in epoxy Kapton-glass panels (image top left), it is the first superconducting toroidal-field coil for the ITER fusion experiment under construction in Cadarache, Southern France. The giant D-shaped ring contains 4.5 km of niobium-tin cable (each containing around 1000 individual superconducting wires) wound into a coil that will carry a current of 68,000 A, generating a peak magnetic field of 11.8 T to confine a plasma at a temperature of 150 million degrees. The coil will soon be joined by 18 others like it, 10 manufactured in Europe and nine in Japan. After completion at ASG, the European coils will be shipped to SIMIC in Italy, where they will be cooled to 78 K, tested and welded shut in a 180 tonne stainless-steel armour. They will then be impregnated with special resin and machined using one of the largest machines in Europe, before being transported to the ITER site.
Science doesn’t get much bigger than this, even by particle-physics standards. ITER’s goal is to demonstrate the feasibility of fusion power by maintaining a plasma in a self-sustaining “ignition” phase, and was established by an international agreement ratified in 2007 by China, the European Union (EU), Euratom, India, Japan, Korea, Russia and the US. Following years of delay relating to the preferred site and project costs, ITER entered construction a decade ago and is scheduled to produce first plasma by December 2025. The EU contribution to ITER, corresponding to roughly half the total cost, amounts to €6.6 billion for construction up to 2020.
Fusion for energy
The scale of ITER’s components is staggering. The vacuum vessel that will sit inside the field coils is 10 times bigger than anything before it, measuring 19.4 m across, 11.4 m high and requiring new welding technology to be invented. The final ITER experiment will weigh 23,000 tonnes, almost twice that of the LHC’s CMS experiment. The new toroidal-field coil is the first major magnetic element of ITER to be completed. A series of six further poloidal coils, a central solenoid and a number of correction coils will complete ITER’s complex magnetic configuration. The central solenoid (a 1000 tonne superconducting electromagnet in the centre of the machine) must be strong enough to contain a force of 60 MN – twice the thrust of the Space Shuttle at take-off.
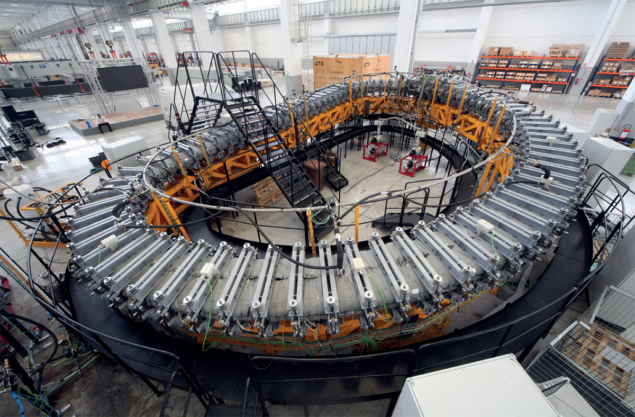
Fusion for Energy (F4E), the EU organisation managing Europe’s contribution to ITER, has been collaborating with industrial partners such as ASG Superconductors, Iberdrola Ingeniería y Construcción, Elytt Energy, CNIM, SIMIC, ICAS consortium and Airbus CASA to deliver Europe’s share of components in the field of magnets. At least 600 people from 26 companies have been involved in the toroid production and the first coil is the result of almost a decade of work. This involved, among other things, developing new ways to jacket superconducting cables based on materials that are brittle and much more difficult to handle than niobium-titanium. In total, 100,000 km of niobium-tin strands are necessary for ITER’s toroidal-field magnets, increasing worldwide production by a factor 10.
Since 2008, F4E has signed ITER-related contracts reaching approximately €5 billion, with the magnets amounting to €0.5 billion. Firms that are involved, such as SIMIC where the coils will be tested and Elytt, which has developed some of the necessary tooling, have much to gain from collaborating in ITER. According to Philippe Lazare, CEO of CNIM Industrial Systems Division: “In order to manufacture our share of ITER components, we had to upgrade our industrial facilities, establish new working methods and train new talent. In return, we have become a French reference in high-precision manufacturing for large components.”
CERN connection
Cooling the toroidal-field magnets requires about 5.8 tonnes of helium at a temperature of 4.5 K and a pressure of 6 bar, putting helium in a supercritical phase slightly warmer than it is in the LHC. But ITER’s operating environment is totally different to an accelerator, explains head of F4E’s magnets project team Alessandro Bonito-Oliva: “The magnets have to operate subject to lots of heat generated by neutron irradiation from the plasma and AC losses generated inside the cable, which has to be removed, whereas at CERN you don’t have this problem. So the ITER coolant has to be fairly close to the wire – this is why we used forced-flow of helium inside the cable.” A lot of ITER’s superconductor technology work was driven by CERN in improving the characteristics of superconductors, says Bonito-Oliva: “High-energy physics mainly looks for very high current performance, while in fusion it is also important to minimise the AC losses, which generally brings a reduction of current performance. This is why Nb3Sn strands for fusion and accelerators are slightly different.”
CERN entered formal collaboration with ITER in March 2008 via a co-operation agreement concerning the design of high-temperature superconducting current leads and other magnet technologies, with CERN’s superconducting laboratory in building 163 becoming one of the “reference” laboratories for testing ITER’s superconducting strands. Niobium-tin is the same material that CERN is pursuing for the high-field magnets of the High Luminosity LHC and also a possible future circular collider, although the performance demands of accelerator magnets requires significant further R&D. Head of CERN’s technology department, Jose Miguel Jimenez, who co-ordinates the collaboration between CERN and ITER, says that in addition to helping with the design of the cable, CERN played a big role in advising for high-voltage testing of the cable insulation and, in particular, with the metallurgical aspect. “Metallurgy is one of the key areas of technology transfer from CERN to ITER. Another is the HTS current leads, which CERN has helped to design in collaboration with the Chinese group working on the ITER tokamak, and in simulating the heat transfer under real conditions,” he explains. “We also helped with the cryoplants, magnetic-field quality, and on central interlocks and safety systems based on our experience with the LHC.”