The UKAEA Materials Research Facility does the heavy-lifting on materials engineering assurance for emerging fusion technologies. Joe McEntee reports.
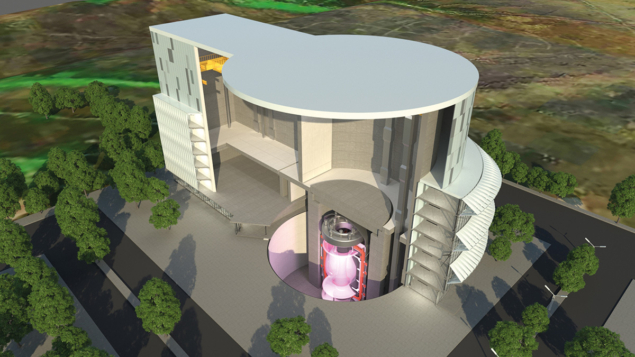
The UK Atomic Energy Authority (UKAEA) is busy shaping a quiet revolution in advanced materials research as part of its fusion R&D roadmap. The goal: to fast-track development of next-generation reactor materials that can withstand the “triple-whammy” of tritium fuel permeation (into “first-wall” components), transmutation (induced radioactivity) and atomic displacement effects (mechanical damage) – all of which represent potential show-stoppers when it comes to the UK’s strategic objective of delivering fusion power into the electricity grid by the middle of the century.
In a signal of intent, the UKAEA completed a £10 million extension of its Materials Research Facility (MRF) at Culham Science Centre, Oxfordshire, at the end of last year. The investment doubled the size of MRF, providing an additional 12 shielded research rooms (used to house high-end analytical instrumentation) and more than 250 m2 of radioactive-capable laboratory space (to investigate enhanced neutron-tolerant materials).
Operationally, a key driver for MRF is the realisation of radiation-hardened materials and platform technologies for the so-called Spherical Tokamak for Energy Production (STEP), a UK prototype fusion energy plant targeting operation in 2040 and, thereafter, a sustainable pathway to commercially viable nuclear fusion (see “Back to basics on STEP”). That’s an ambitious timeline – and one currently preoccupying the project team sweating the details for STEP’s four-year, £220 million design phase (due for completion by mid-2024).
Back to basics on STEP
• In the prototype STEP power plant (artist rendering shown above), nuclear fusion will be realised in a spherical tokamak device that uses superconducting magnets to confine and control a hot plasma of fusion fuels in a torus configuration.
• At the heart of it all is the fusion reaction between deuterium and tritium nuclei, yielding one helium nucleus, one neutron and, in the process, liberating huge amounts of thermal energy for electricity production. STEP is aiming to generate 100 MW of net electricity as the demonstration of a commercially relevant plant.
• While most of today’s experimental fusion devices – including JET at Culham and the work-in-progress ITER project in southern France – are built in the shape of a ring doughnut, STEP’s spherical plant will be shaped more like a cored apple. This spherical tokamak design is expected to minimise STEP’s physical footprint, improve operating efficiency, as well as potentially reduce capital and running costs.
With this in mind, the MRF offers a focal point for R&D collaboration, bringing together academic and industrial researchers, as well as experimentalists and modellers, to address materials gaps in the STEP programme and to foster innovative approaches to materials qualification for fusion. By extension, the MRF also provides workers with specialist experience to support users with their sample preparation and analysis, plus logistics advice for the transport of radioactive materials.
A case study in this regard is the £2 million MRF FaSCiNATe initiative (or, to give it its full name – Facility for the Structural Characterisation of materials for Nuclear Applications operating at high Temperatures). Headed up by UKAEA in partnership with the University of Oxford and the University of Birmingham, FaSCiNATe provides what UKAEA claims is “a unique and complementary suite of scientific instruments” to characterise the thermal stability of microstructural damage in neutron-irradiated materials and the associated effects on mechanical properties.
Specifically, FaSCiNATe focuses on the materials defects resulting from irradiation damage: what strain they create (as measured by high-temperature X-ray diffraction), what energy they store (using high-vacuum differential scanning calorimetry), and what influence they have on mechanical behaviour at the micron scale (using an in situ mechanical test stage mounted inside an electron microscope).
“The FaSCiNATe instruments are integrated in shielded environments and equipped with robotic sample mounting systems to remotely insert and retrieve radioactive samples,” explains Andy London, scientific lead for active testing at MRF. “Being able to predict materials degradation under neutron irradiation will help us to extend the lifetime of existing nuclear reactors as well as inform the materials requirements of future fission and fusion reactors.”
The in situ load frame, for example, enables researchers to observe how materials deform at fusion-relevant operational temperatures (–160 to 1000 °C), yielding insights for designer materials that prevent the accumulation of more serious damage. Meanwhile, the heating of defective materials can actually cause atoms to rearrange and therefore “heal” some of the irradiation damage, releasing energy in the process. High-vacuum differential scanning calorimetry is able to quantify these energy changes as a function of temperature, while X-ray diffraction tracks the evolution of defect strain at the atomic scale as it recovers with increasing temperatures.